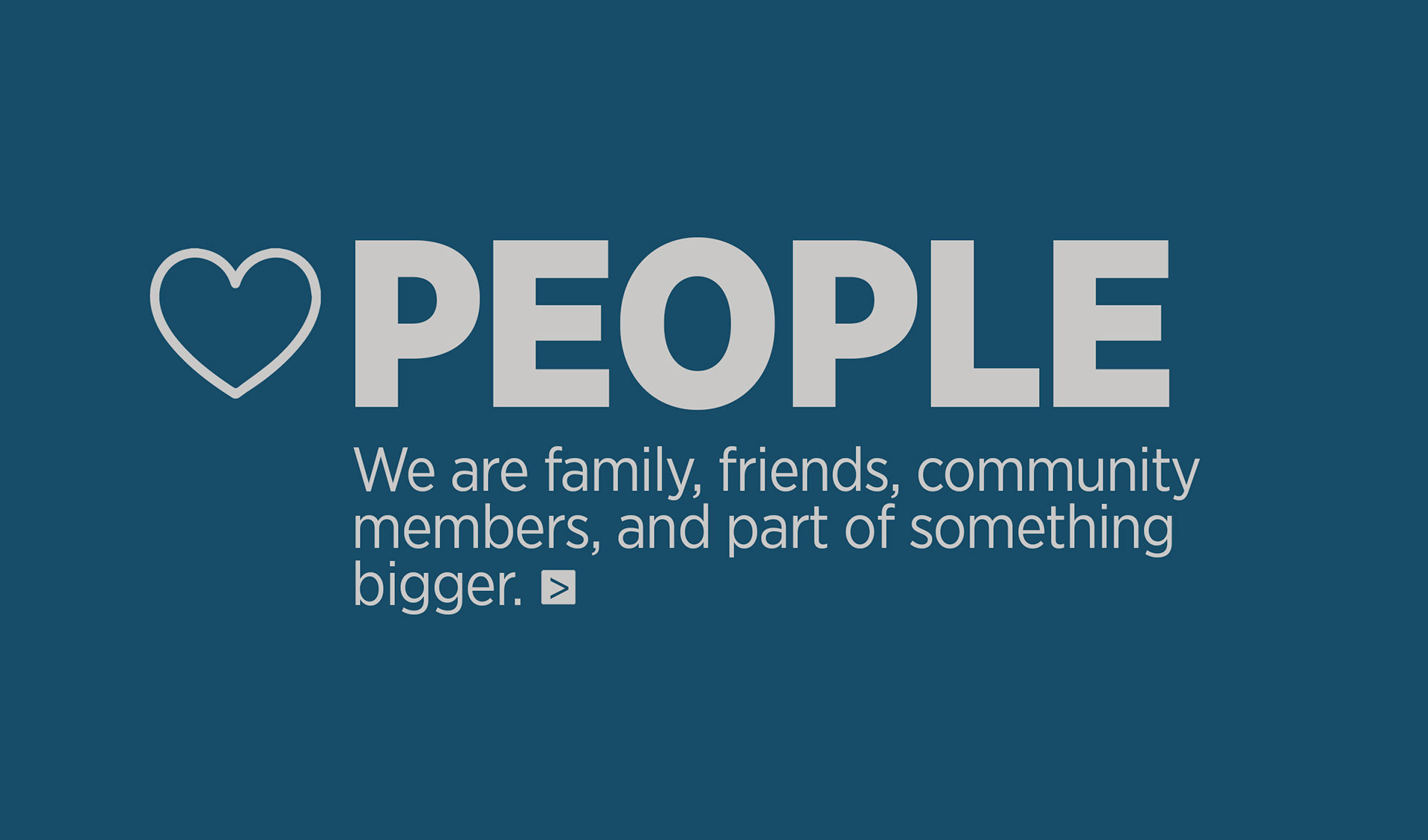
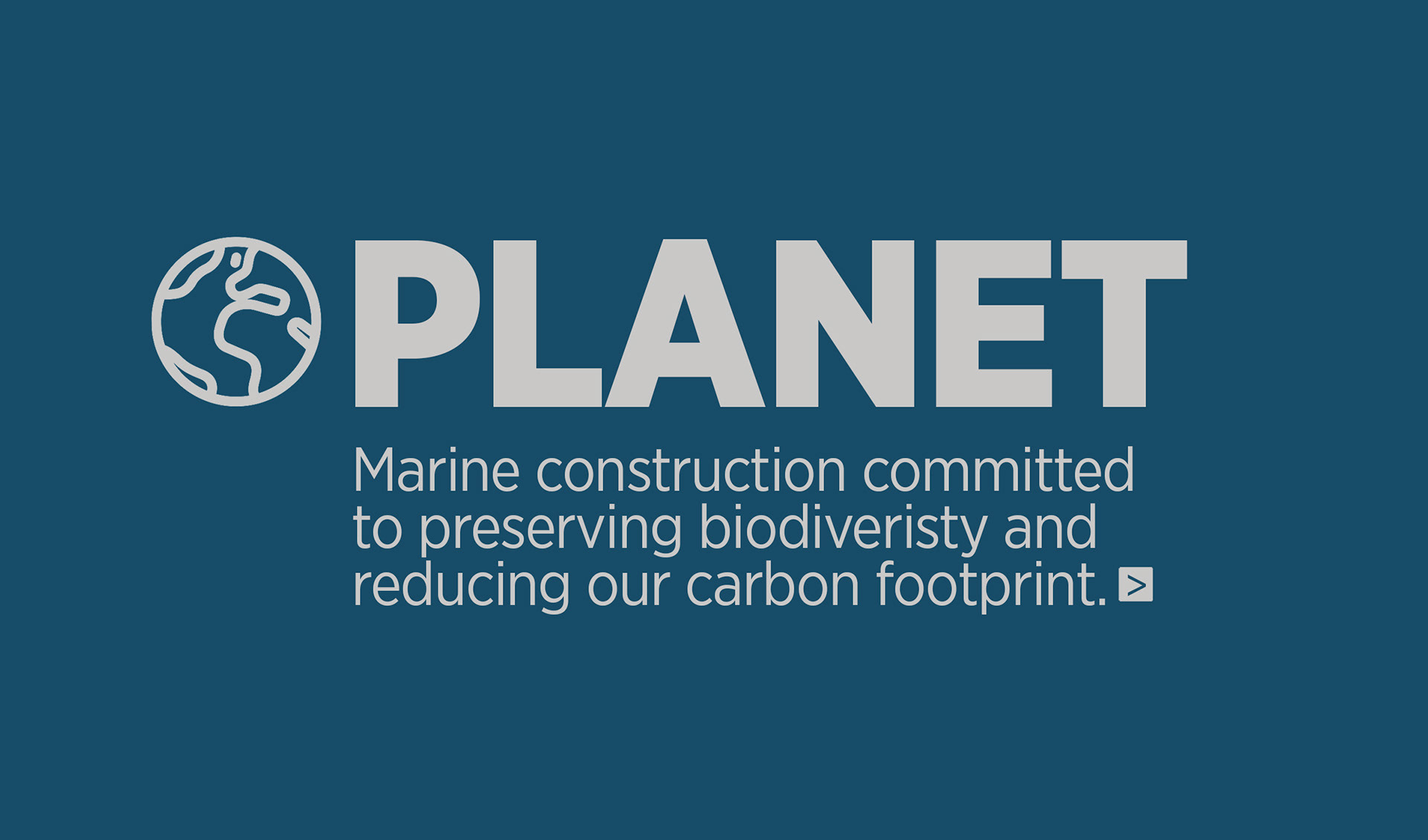
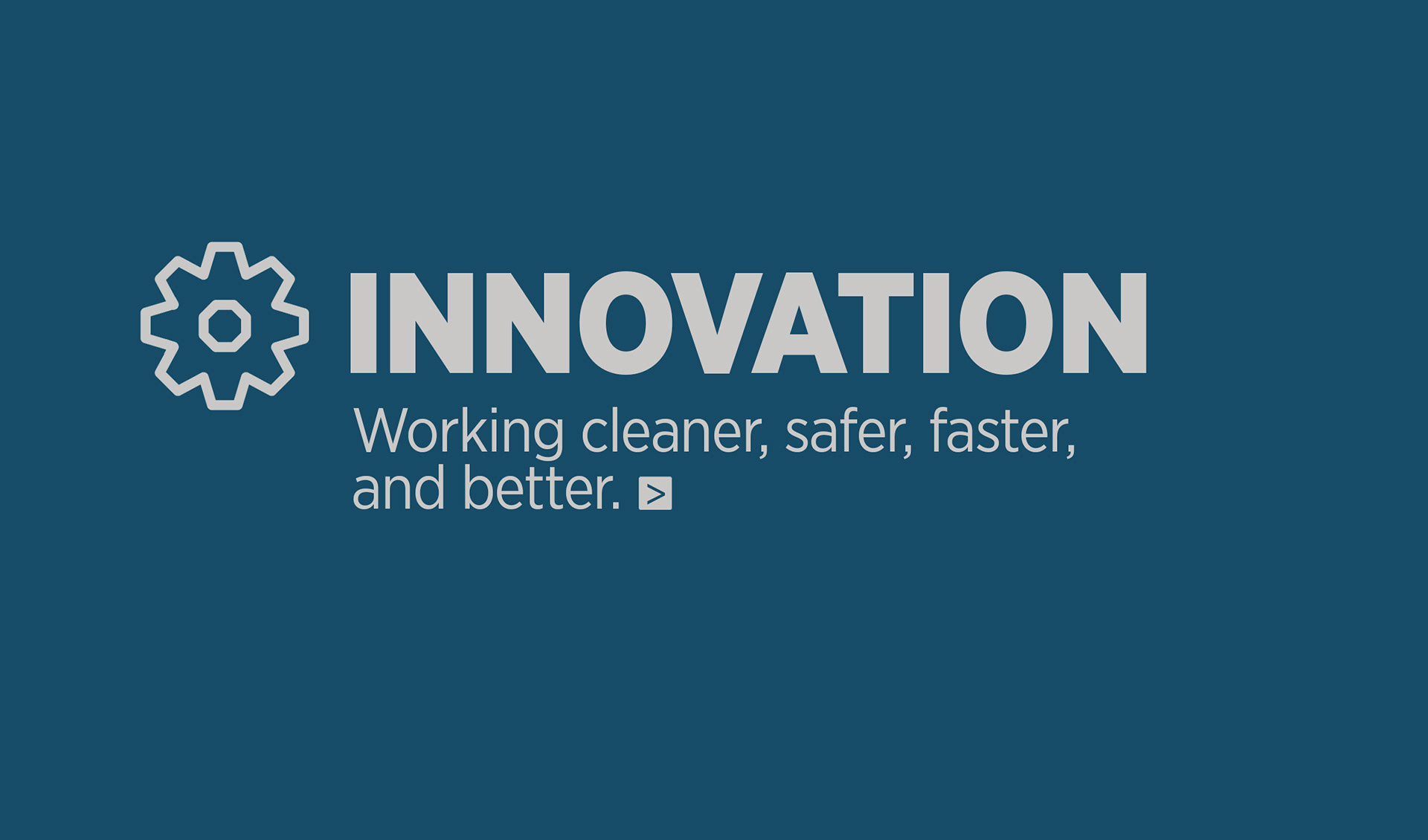
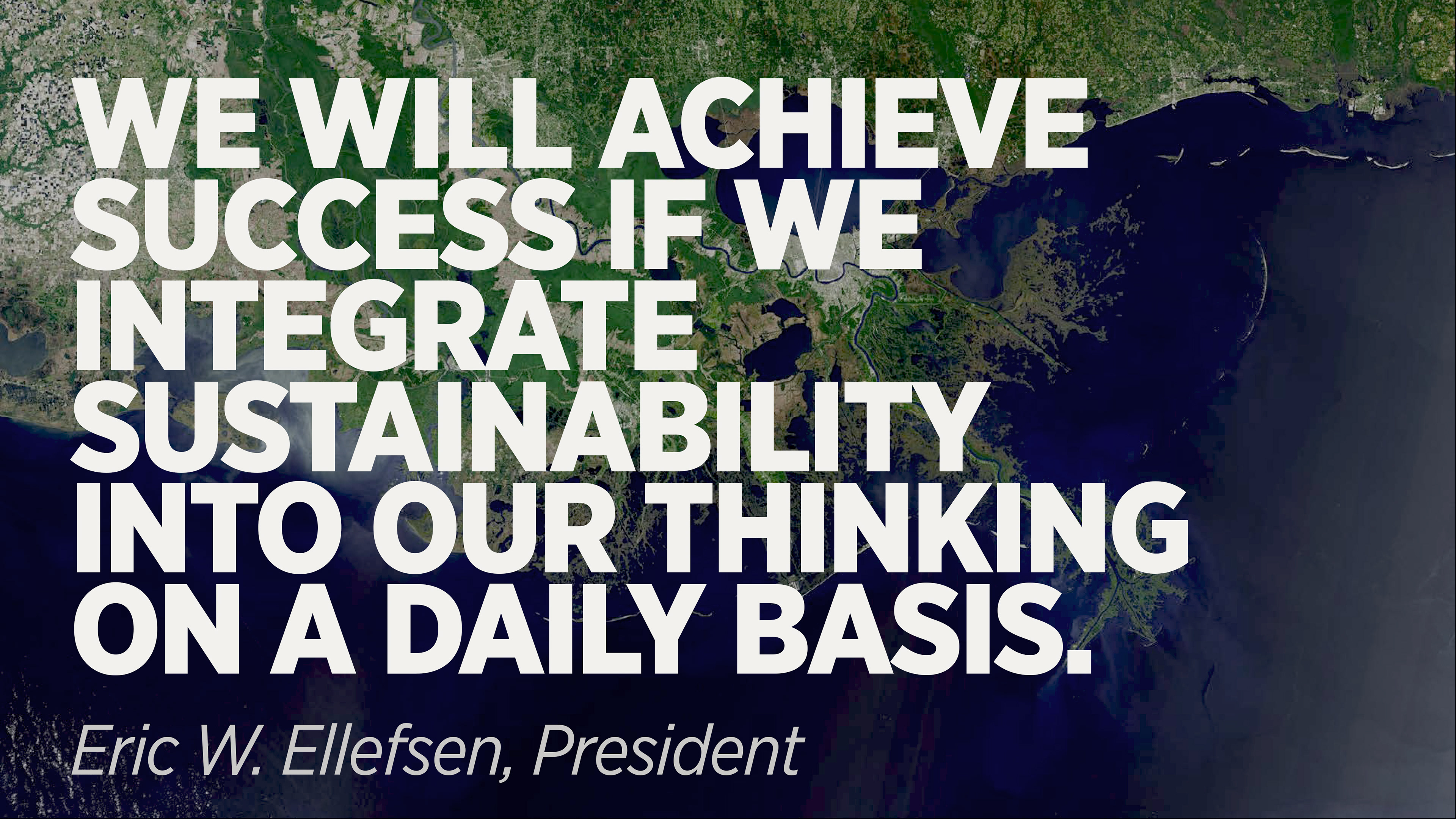
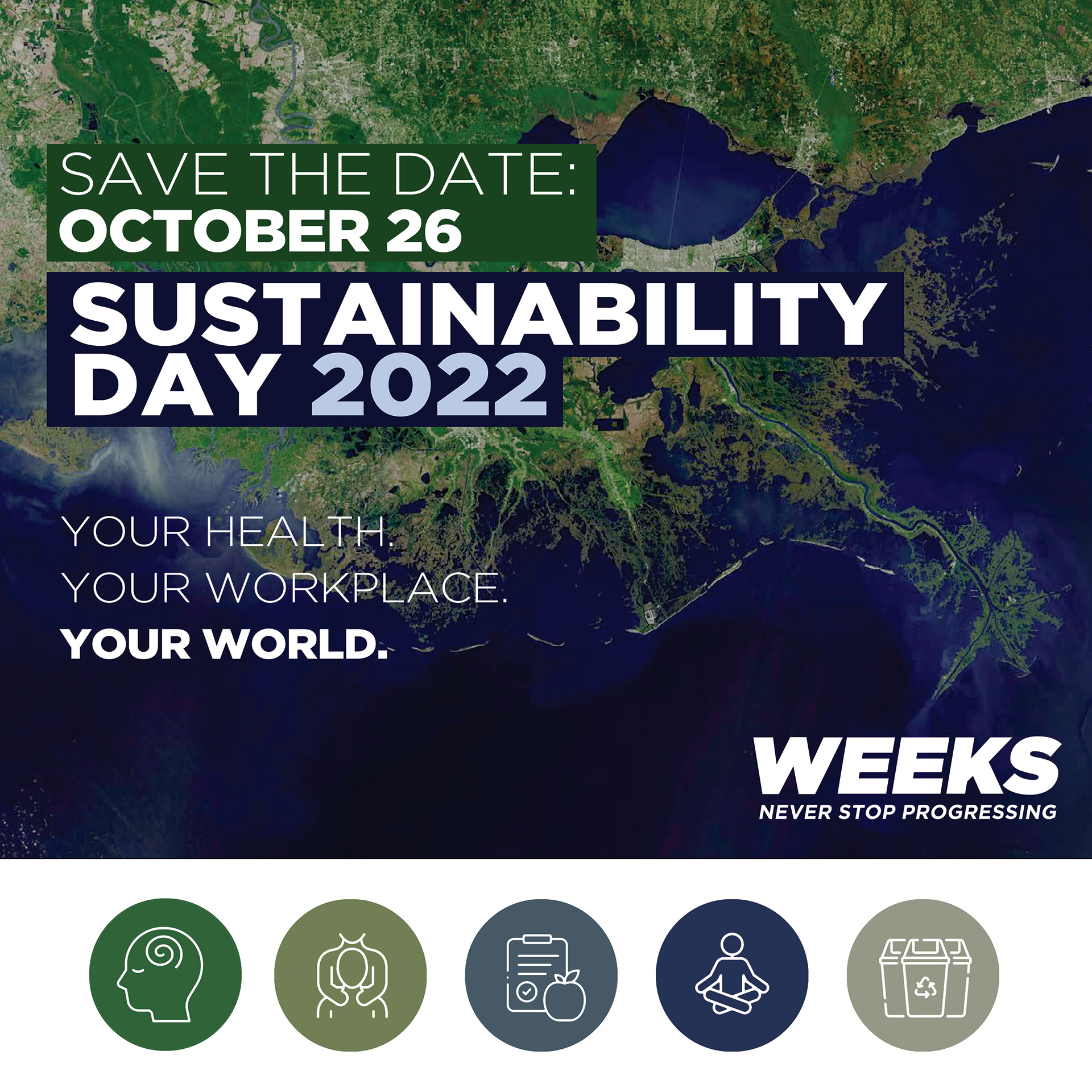
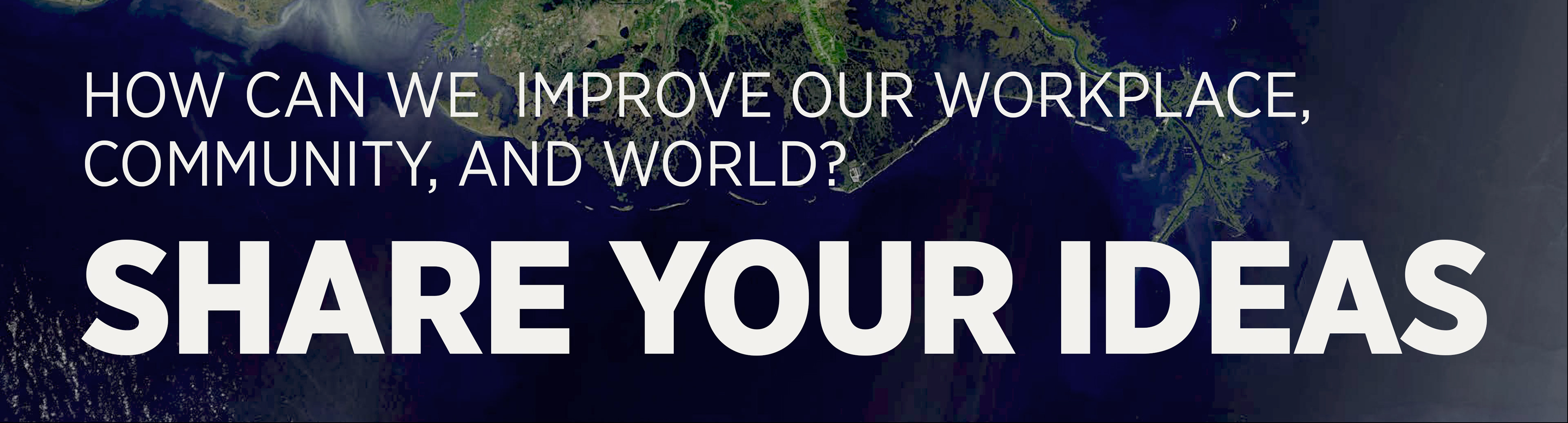

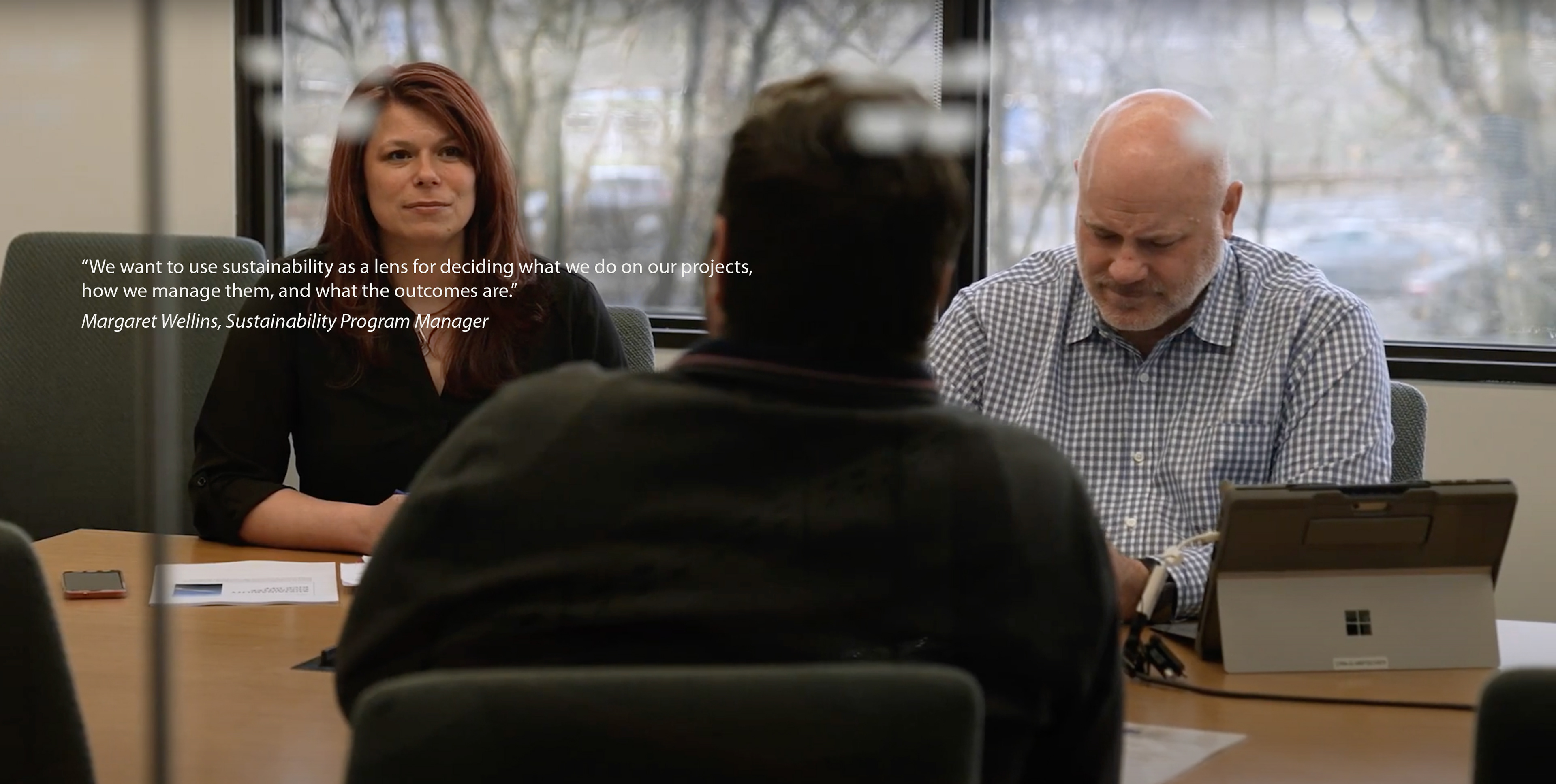
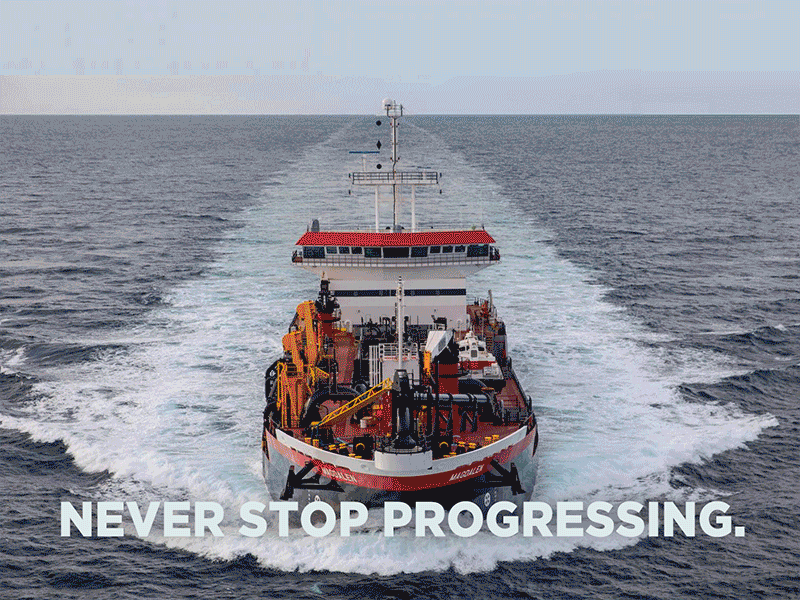
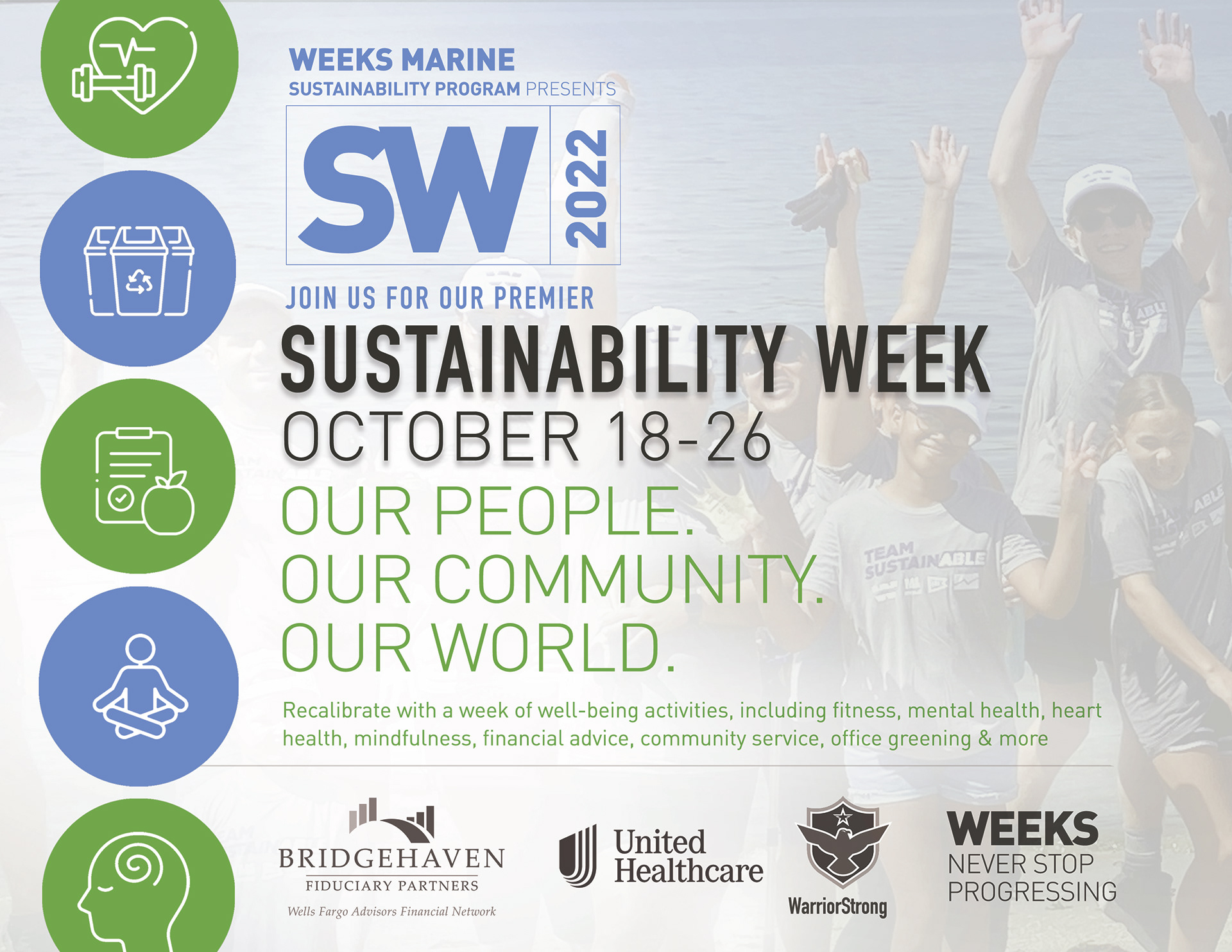
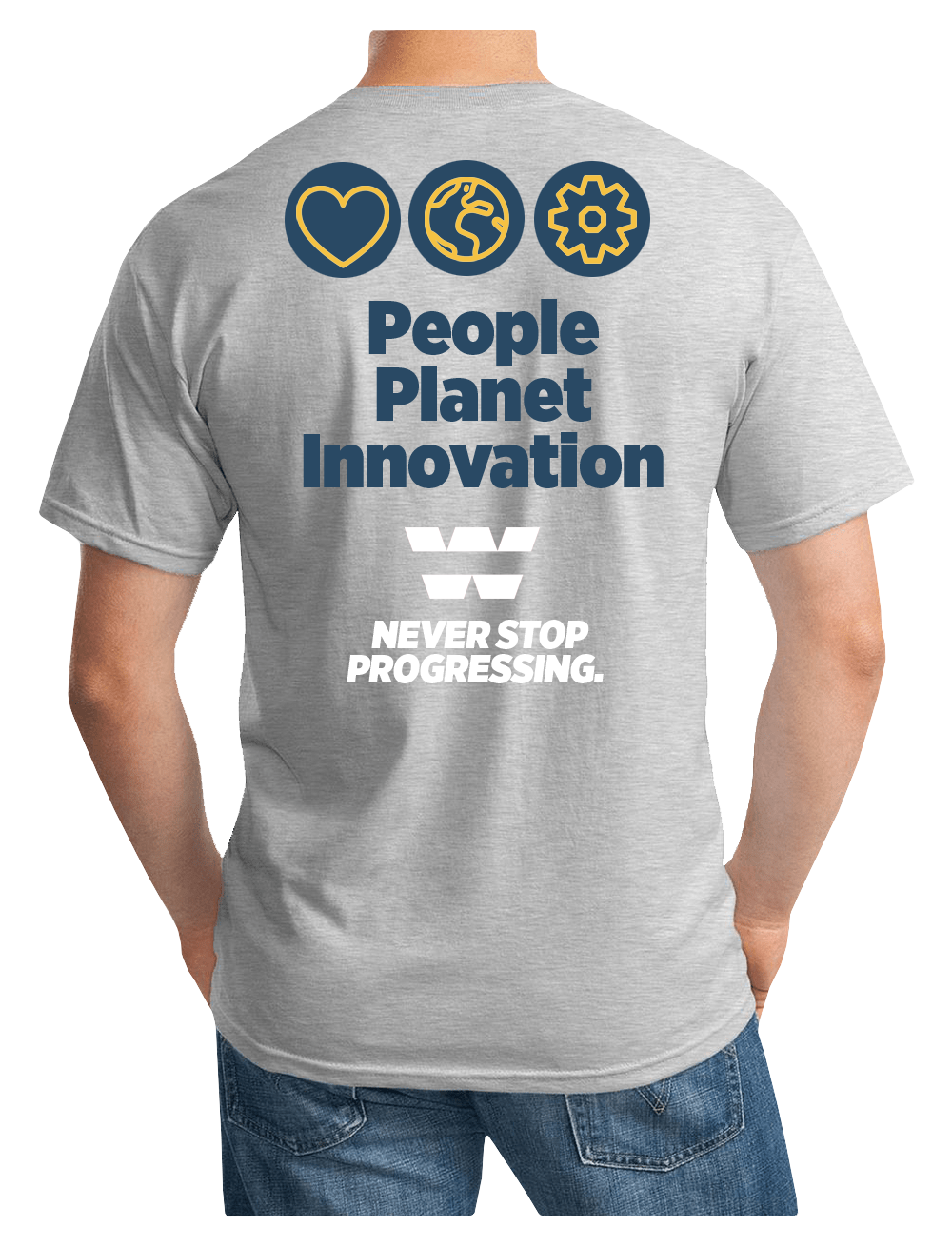
Writing samples from the Weeks Marine Sharepoint Site
About
Our operations affect the environment. We consume a lot of resources including water, energy and materials. That's the nature of our work. But that does not mean we cannot integrate sustainability into our thinking on a daily basis. After all, our line of work is at ground zero of climate change.
Between sea level rise and more frequent extreme weather events hitting our waterfronts, our work is more important than ever in providing resilient infrastructure, functional waterways, and mission-critical solutions in the marine environment. With changes in the industry and more clients looking for can-do firms with sustainable solutions, we are well positioned. We are already committed to the highest standards for environmental compliance at all of our facilities and on our projects.
But there is still a lot more we can be doing. The Sustainability Program builds on our legacy and helps to guide our growth into the future. This is 100% business pillared on People, the Planet, and Innovation--as it should be.
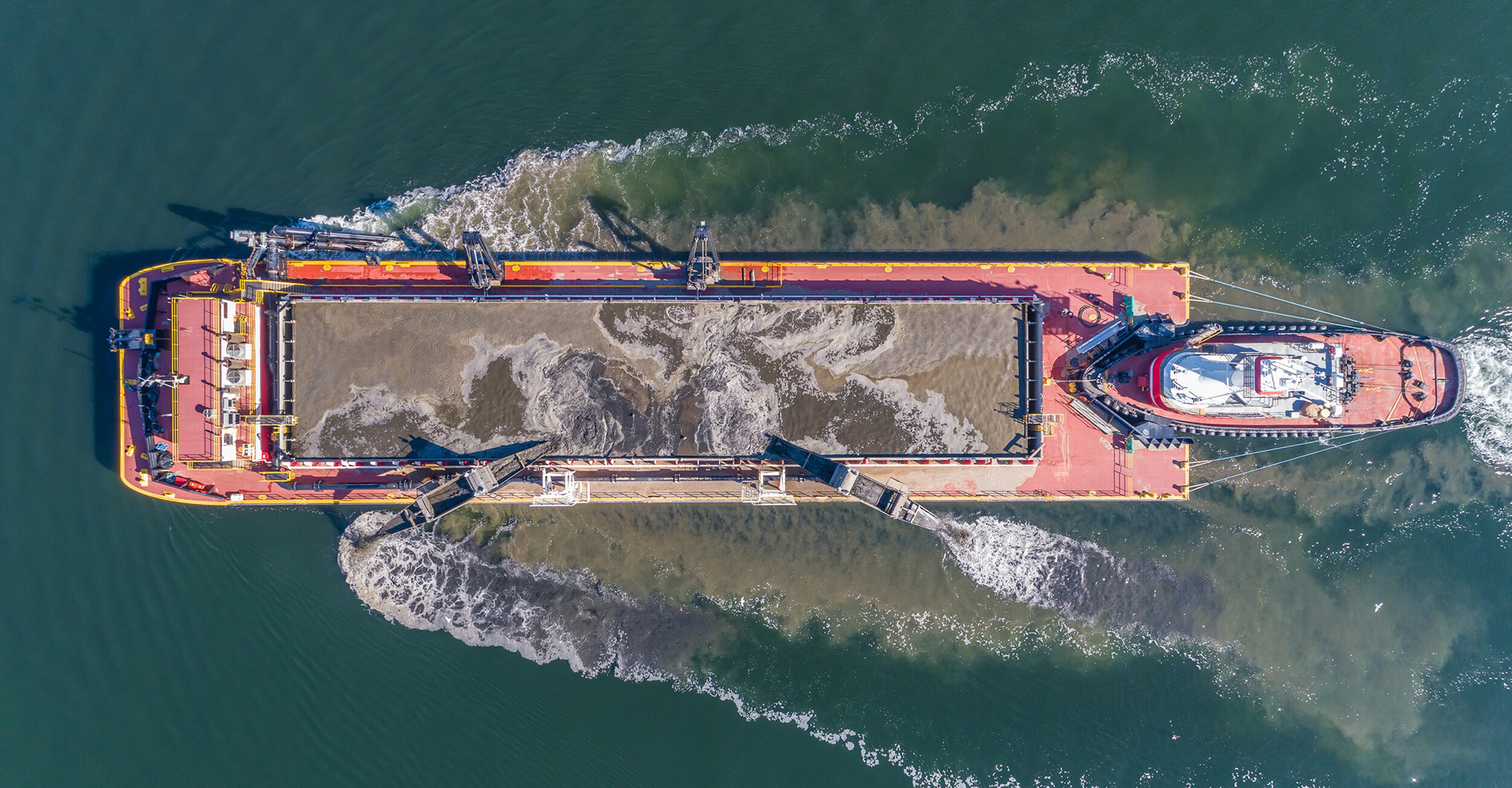
North American Aggregates
Getting Granular on Sustainability
When most people think of sustainability, an industrial sand processing plant, particularly one built on an environmental catastrophe, is not the first thing that comes to mind.
But the origin story of North American Aggregates, from acquisition of a property in Perth Amboy, NJ to launching a state-of-the-art energy-efficient sand processing facility deserves a more granular telling if we are to appreciate the depth of problem-solving and care that goes into sustainable business growth at Weeks.
Our story begins in 2015 with the search for a home for our prospective business venture. The sand from the Ambrose Federal Navigation Channel, serving lower New York Bay is naturally replenished by the ocean currents and has been a sustainable source of building material for the Tri-State for decades. If we find the right location for a processing plant along lower New York Bay, we could efficiently serve the Tri-State area.
But the big problem is the Tri-State area is worth more as a warehouse for Amazon, a box store, or high-end residential property than a working waterfront. As a result, industrial maritime sites are disappearing along the urban coastline. To make matters worse there is also a global shortage of construction sand. Upland sources are getting depleted. Environmental concerns are growing.
Although we are not running out of aquatic sources for sand, the economic reality is the harder it is to get, the more costly it becomes. This is all the more reason to take the 100-year-old planners’ dictum to heart, ‘act locally, think globally’.
Right from the get-go, we had to think sustainably recognizing that a local operation drawing on local natural resources means faster processing and delivery time, that’s less CO2 emissions and vulnerable supply chains, and a more resilient region in terms of having protected valuable infrastructural resources. So, we had to make this work even if it meant buying a property that no one wants, and that’s what we did.
In 2015 we found a fallow contaminated site in the northern most area of Perth Amboy. Formerly owned by Hess from 1952 to 1994, the site was an environmental ruin. In 1990 a piling failure resulted in the accidental release of one million gallons of No. 6 fuel oil. That triggered the Industrial Site Recovery Act (ISRA) which required Hess to clean up and remediate the site. The property remained largely unused, until it was bought by Vopak in 2011. As Vopak was designing a new terminal and Hess was remediating the property, Hurricane Sandy hit, flooding the site and causing another 300,000-gallon oil spill from the Shell/Motiva terminal just north. At that point Vopak threw in the towel, sold the property to Kindred Morgan, and the site went fallow again until Weeks came on the scene.
For us, the price was right. Hess had the remediation under control. The location was perfect, nested along the Arthur Kill and Woodbridge Creek. We had industrial neighbors to the north and south, so we didn’t have to worry about nearby residents getting their property sandblasted on windy days - a serious issue that contributed to the closure of Amboy Aggregates.
But there was a catch. Hess was concerned that our operation would impede their remediation because they believed we couldn’t cap the site adequately, in the way a massive warehouse or box store could.
We had to get creative. At the time we were involved in the decommissioning and deconstruction of the Tappan Zee Bridge. So, we recycled the concrete demolition material used from the road decking and foundation of the bridge and turned that into the clean-fill cap.
We stripped the steel from the concrete and crushed to 6”, then used this to raise the site elevation to +16’ above mean low water, satisfying both Hess and new flood hazard standards. We also put in a new 650’ bulkhead along the site making the site more resilient than ever. We were able to get what we needed done on the site with a really quick turnaround time.
In 2016 we closed on the property and the following year we created North American Aggregates, a wholly owned subsidiary of Weeks Marine, that is specifically designed to process materials on the site.
Radically reducing our carbon footprint, we built an innovative sand processing facility that runs 100% on electric, drawing exclusively from the grid. All the conveyors are electric, the surge tunnels and gates are pneumatic. We replaced our traditional cable cranes with E-Cranes that run entirely on electric. For perspective, the traditional cable crane ran for approximately 384 hours/month offloading the Eleanor. That’s equivalent to 2884 metric tons of CO2e emissions/year, or 527 gasoline-powered passenger vehicles driven for one year. Once the E-Cranes were installed our direct emissions from offload went to zero. Additionally, while the cable crane took 12-16 hours to offload, the E-Cranes do it in 5.5-7 hours. [1]
Our approvals with the New Jersey Department of Environment Protection (NJDEP) and Army Corp of Engineers enables us to mine naturally replenishing materials at the easternmost section of the Ambrose Federal Navigation channel. Rather than casting the dredge material out to sea as is often done, we turn it into high-quality sand. We deliver the sand in large part by barge, taking hundreds of trucks off the road a week, improving air quality, reducing carbon emissions, and traffic.
When all is said and done, we took a contaminated fallow site and put it back to use while creating 50 new jobs. We cemented win/win arrangements across the board. The Army Corp of Engineers gets free maintenance dredging of the channel into the Port of New York and New Jersey, NJDEP gets a royalty twice a year on material mined, and the Tri-State area gets sand for use in the concrete, asphalt, and the general fill market that is locally sourced, locally processed, low-cost, and sustainably delivered.
For our part, we established North American Aggregate as a leader in the aggregate market in the Tri-State area and an inspiration to our Sustainability Program and beyond.
[1] CO2e (e for equivalent) is the universal unit of measurement used to indicate the global warming potential of greenhouse gases. We used the Green Teams' emissions calculator to quantify CO2e output of the traditional cable crane. As we work with more sustainability-minded clients, our ability to track our CO2 emissions and that of a proposed project will help us strengthen partnerships and contribute to sustainable growth.